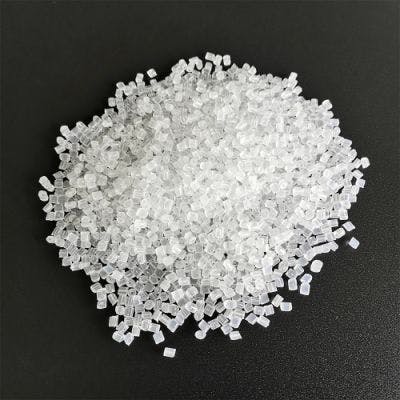
PP (Polypropylene)
Polypropylene (PP), also known as polypropene, is a thermoplastic polymer used in a wide variety of applications. It is produced via chain growth polymerization from the monomer propylene.
Polypropylene belongs to the group of polyolefins and is partially crystalline and non-polar. Its properties are similar to polyethylene, but it is slightly harder and more heat-resistant. It is a white, mechanically rugged material and has a high chemical resistance. Polypropylene is the second-most widely produced commodity plastic and is often used in packaging and labeling.
Polypropylene is in many aspects similar to polyethylene, especially in solution behavior and electrical properties. The methyl group improves mechanical properties and thermal resistance, although the chemical resistance decreases. The properties of polypropylene depend on the molecular weight and molecular weight distribution, crystallinity, type and proportion of comonomer (if used) and the isotacticity. In isotactic polypropylene, for example, the methyl groups are oriented on one side of the carbon backbone.
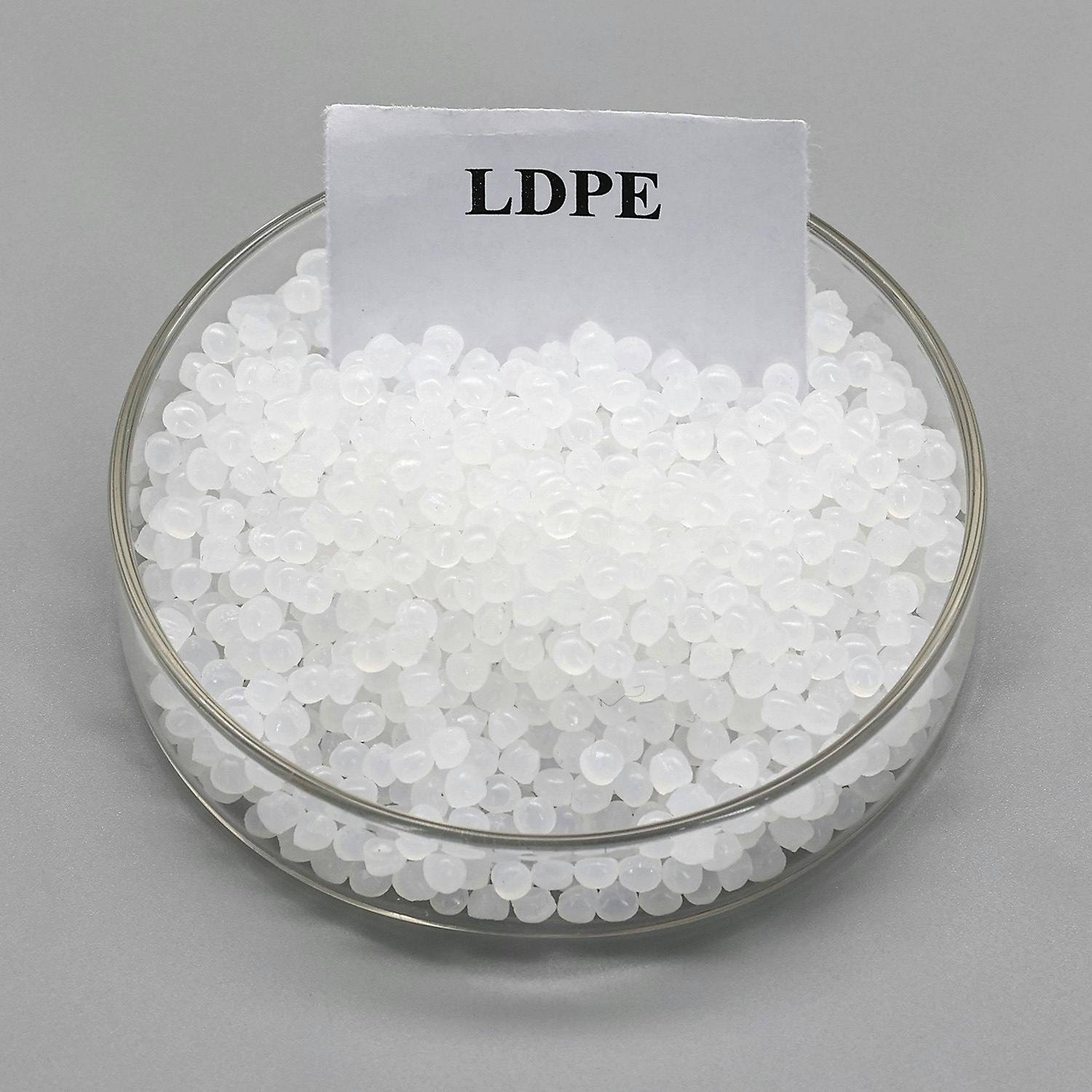
LDPE
LDPE is a thermoplastic made from the monomer ethylene. It was the first grade of polyethylene, produced by Imperial Chemical Industries (ICI) using a high pressure process via free radical polymerisation. Its manufacture employs the same method today. The EPA estimates 5.7% of LDPE is recycled in the United States. Despite competition from more modern polymers, LDPE continues to be an important plastic grade.
LDPE is defined by a density range of 917–930 kg/m3.[6] At room temperature it is not reactive, except to strong oxidizers; some solvents cause it to swell. It can withstand temperatures of 65 °C (149 °F) continuously[6] and 90 °C (194 °F) for a short time. Made in translucent and opaque variations, it is quite flexible and tough.
LDPE has more branching (on about 2% of the carbon atoms) than HDPE, so its intermolecular forces are weaker, its tensile strength is lower, and its resilience is higher. The side branches mean that its molecules are less tightly packed and less crystalline, and therefore its density is lower.
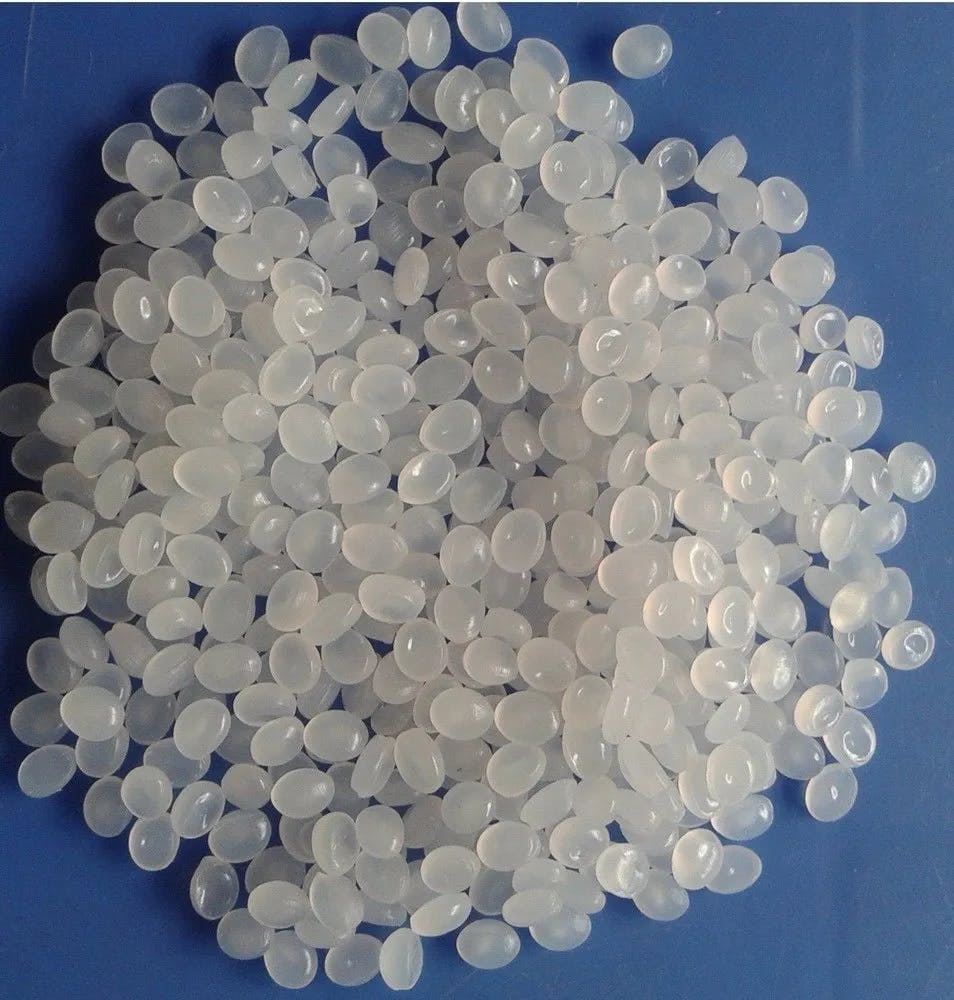
LLDPE
LLDPE is a substantially linear polymer, with significant numbers of short branches, commonly made by copolymerisation of ethylene with longer-chain olefins. Linear low-density polyethylene differs structurally from conventional LDPE because of the absence of long chain branching. The linearity of LLDPE results from the different manufacturing processes of LLDPE and LDPE. In general, LLDPE is produced at lower temperatures and pressures by copolymerization of ethylene and such higher alpha olefins as butene, hexene, or octene. The copolymerization process produces an LLDPE polymer that has a narrower molecular weight distribution than conventional LDPE and in combination with the linear structure, significantly differen rheological properties.
The production of LLDPE is initiated by transition metal catalysts, particularly Ziegler or Philips types of catalyst. The actual polymerization process can be done either in solution phase or in gas phase reactors. Usually, octene is the comonomer in solution phase while butene and hexene are copolymerized with ethylene in a gas phase reactor. LLDPE has higher tensile strength and higher impact and puncture resistance than does LDPE. It is very flexible and elongates under stress. It can be used to make thinner films, with better environmental stress cracking resistance. It has good resistance to chemicals. It has good electrical properties. However, it is not as easy to process as LDPE, has lower gloss, and narrower range for heat sealing.

HDPE
HDPE is known for its high strength-to-density ratio. The density of HDPE ranges from 930 to 970 kg/m3. The standard method to test plastic density is ISO 1183 part 2 (gradient columns), alternatively ISO 1183 part 1. Although the density of HDPE is only marginally higher than that of LDPE, HDPE has little branching, giving it stronger intermolecular forces and tensile strength (38 MPa versus 21 MPa) than LDPE. The difference in strength exceeds the difference in density, giving HDPE a higher specific strength. It is also harder and more opaque and can withstand somewhat higher temperatures (120 °C/248 °F for short periods). High-density polyethylene, unlike polypropylene, cannot withstand normally required autoclaving conditions. The lack of branching is ensured by an appropriate choice of catalyst and reaction conditions.
The physical properties of HDPE can vary depending on the molding process that is used to manufacture a specific sample; to some degree, a determining factor is the international standardized testing methods employed to identify these properties for a specific process. For example, in rotational molding, to identify the environmental stress crack resistance of a sample, the notched constant tensile load test (NCTL) is put to use.
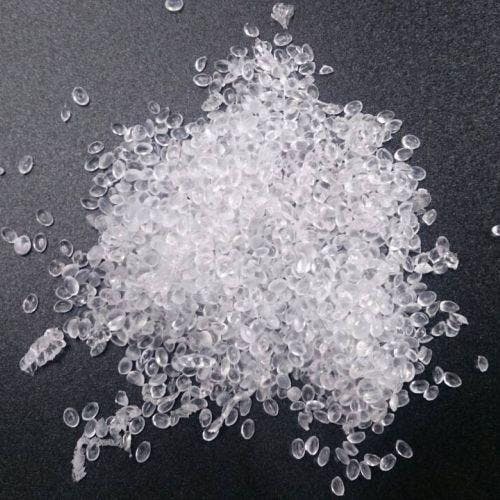
EVA
Ethylene-vinyl acetate (EVA), also known as poly (ethylene-vinyl acetate) (PEVA), is a copolymer of ethylene and vinyl acetate. The weight percent of vinyl acetate usually varies from 10 to 40%, with the remainder being ethylene. There are three different types of EVA copolymer, which differ in the vinyl acetate (VA) content and the way the materials are used.
The EVA copolymer which is based on a low proportion of VA (approximately up to 4%) may be referred to as vinyl acetate modified polyethylene. It is a copolymer and is processed as a thermoplastic material – just like LDPE. It has some of the properties of a low-density polyethylene but increased gloss (useful for film), softness and flexibility. The material is generally considered non-toxic.
The EVA copolymer, which is based on a medium proportion of VA (approximately 4 to 30%), is referred to as thermoplastic ethylene-vinyl acetate copolymer and is a thermoplastic elastomer material. It is not vulcanized but has some of the properties of a rubber or of plasticized polyvinyl chloride particularly at the higher end of the range. Both filled and unfilled EVA materials have good low temperature properties and are tough. The materials with approximately 11% VA are used as hot-melt adhesives.
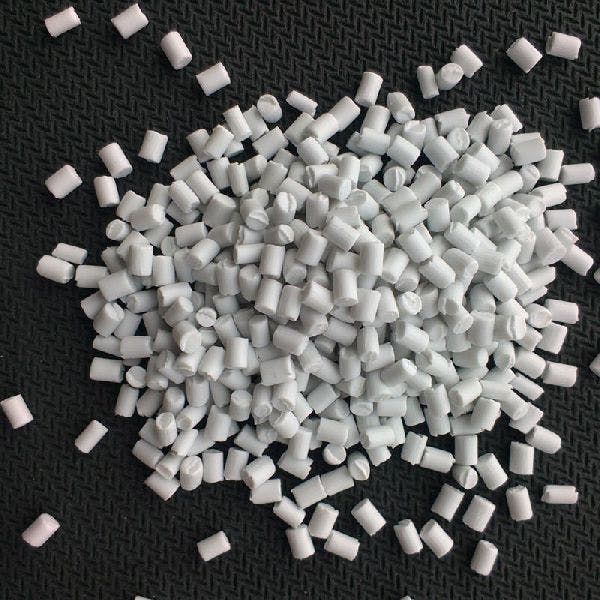
PVC
Polyvinyl chloride (alternatively: poly(vinyl chloride), polyvinyl, or simply vinyl is the world's third-most widely produced synthetic polymer of plastic. About 40 million tons of PVC are produced each year.
PVC comes in two basic forms: rigid (sometimes abbreviated as RPVC) and flexible. The rigid form of PVC is used in construction for pipe and in profile applications such as doors and windows. It is also used in making plastic bottles, non-food packaging, food-covering sheets and plastic cards (such as bank or membership cards). It can be made softer and more flexible by the addition of plasticizers, the most widely used being phthalates. In this form, it is also used in plumbing, electrical cable insulation, imitation leather, flooring, signage, phonograph records, inflatable products, and many applications where it replaces rubber. With cotton or linen, it is used in the production of canvas. Pure polyvinyl chloride is a white, brittle solid. It is insoluble in alcohol but slightly soluble in tetrahydrofuran.